A feed extruder is a machine that uses high temperature and pressure to puff and shape raw materials. It's widely used for producing expanded feeds such as pet food and fish feed. Powered by a screw mechanism, the raw material is pushed through a die, where it's heated, expanded, and formed. This process improves feed palatability and enhances nutrient absorption, making the extruder an essential tool in modern feed production.
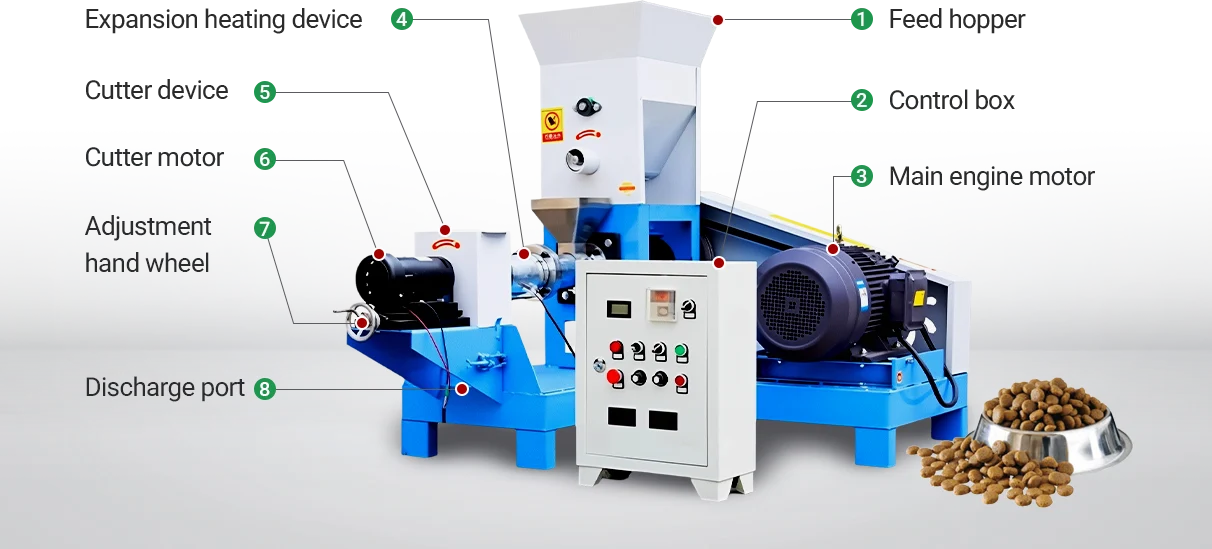
Advantages of the Feed Extruder
-
Improved palatability: The extrusion process enhances the texture and flavor of the feed. It also promotes starch gelatinization and breakdown, encouraging animals to eat more while improving digestion and nutrient uptake.
-
Easier digestion and absorption: High temperature and pressure destroy plant cell walls and reduce crude fiber content. As a result, animals can absorb more nutrients more easily.
-
Enhanced feed hygiene: The high temperature and pressure during extrusion effectively eliminate mold, bacteria, and fungi in the raw materials. This significantly improves feed hygiene and helps reduce the risk of diarrhea, enteritis, and other digestive diseases in animals.
-
Less water pollution: Aquatic extruded feed floats or sinks slowly and doesn't dissolve easily. This helps reduce leftover fermentation and prevents water pollution caused by feed breakdown, supporting a more stable farming environment.
-
Longer shelf life: During extrusion, oils are released and form stable lipid complexes. This improves fat utilization and slows down rancidity, allowing the feed to be stored for longer periods.
Beyond the benefits of the extrusion process itself, our feed extruder is also well-designed on the hardware side:
-
The screw and sleeve are made from high-temperature, wear-resistant alloy steel. They are heat-treated for improved durability and longer service life.
-
A single-screw design keeps the structure compact. It uses fewer parts, which means fewer failures and easier cleaning and maintenance.
-
The extruder has an extended screw and barrel. This increases retention and heating time for more thorough expansion.
-
Core components are carefully selected for durability. This helps lower long-term operating costs while keeping the price competitive-without compromising quality.
-
Equipment parameters and die specifications can be customized as needed. Technical support and after-sales service are available to ensure reliable long-term operation.
Product Parameters
Model |
Capacity (kg/h) |
Host power (kw) |
Feeding power (kw) |
Cutting power (kw) |
Machine size (mm) |
Weight (kg) |
KP-40 |
40-60 |
5.5/7.5 |
0.4 |
0.4 |
1200*900*1100 |
300 |
KP-50 |
60-80 |
7.5 |
0.4 |
0.4 |
1300*950*1150 |
350 |
KP-60 |
100-150 |
15 |
0.4 |
0.4 |
1350*1000*1200 |
400 |
KP-70 |
150-200 |
18.5 |
0.4 |
0.4 |
1350*1100*1200 |
460 |
KP-80 |
200-250 |
22 |
0.55 |
0.55 |
1550*1100*1200 |
550 |
KP-90 |
250-300 |
30 |
1.1 |
1.5 |
1750*1450*1300 |
800 |
KP-100 |
300-400 |
37 |
1.1 |
1.5 |
1850*1550*1500 |
950 |
Product Information Download
FAQ?
What's the difference between extruded and regular pellets?
Extruded feed is lighter, crispier, and easier to digest. It offers better palatability and is ideal for fish, pets, and young animals. Regular pellets are harder and more suitable for livestock and poultry.
What raw materials can the extruder process?
It works with a wide range of common feed ingredients, including corn, soybean meal, wheat flour, rice bran, fish meal, and other mixed meals.
Is this a dry or wet extruder? What's the difference?
Ours is a dry-type extruder that doesn't require steam. It's easy to operate and well-suited for small and medium-scale users. Wet extruders use steam for fuller expansion but come with higher cost and complexity. (Custom wet-type options are available upon request.)
Need Some Help?
Contact us quickly and we will reply you within 24 hours. We will not disclose your information.